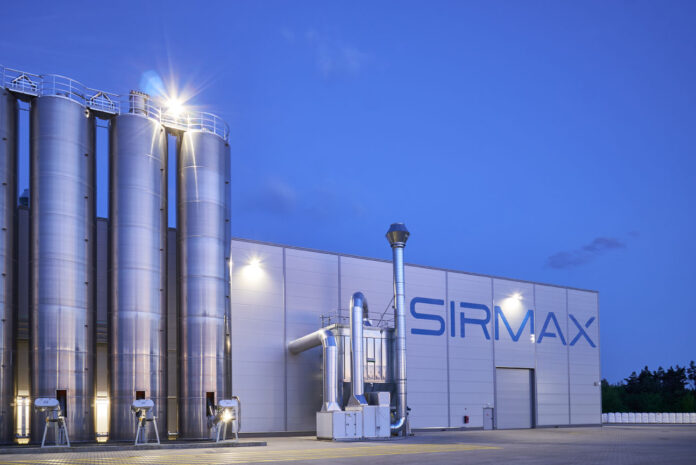
Grupa Sirmax z siedzibą w Cittadella (prow. Padwy) jest jednym z pierwszych na świecie i pierwszym niezależnym europejskim producentem mieszanek polipropylenowych, technopolimerów, mieszanek poużytkowych i biomasy, wykorzystywanych w różnych branżach: motoryzacyjnej, AGD, energetycznej gospodarstwa domowego, elektrycznej, elektronicznej, budowlanej, meblarskiej. O sukcesie tej włoskiej firmy, która ma w Polsce dwa ważne zakłady, rozmawiamy z Massimo Pavinem, prezesem Grupy Sirmax.
Czy może nam pan powiedzieć kilka słów o Sirmax?
Działająca od lat 60. firma posiada 13 zakładów produkcyjnych: sześć we Włoszech, dwa w Polsce (otwarte w 2006 i 2019), jeden w Brazylii (2012), dwa w USA (2015 2020), dwa w Indiach (2017), biuro sprzedaży w Mediolanie, oddziały zagraniczne we Francji, Hiszpanii i Niemczech. Sirmax zdobył znaczące udziały w rynku europejskim, obu Ameryk i azjatyckim, stając się tym samym globalnym producentem na rynku międzynarodowym. Naszymi klientami są Whirlpool, Bosch- Siemens, Electrolux, Karcher, Philips, Honeywell, ABB, Technogym, Stellantis, Volkswagen Group, Daimler, De’ Longhi, Haier, BMW, Audi. W 2021 roku grupa Sirmax odnotowała obroty w wysokości 480 milionów euro, zatrudnia ponad 800 przedstawicieli na całym świecie. Nazwa Sirmax powstała w wyniku połączenia dwóch innych: „Sirte” i „Maxplast”. Od 1999 r. Sirte i Maxplast działają pod wspólną własnością, po fuzji obu firm, pod nazwą Sirmax Spa (S.A.). Od 2004 roku rozpoczęto wdrażanie strategii wzrostu do poziomu globalnego: począwszy od nowego zakładu we Włoszech w Tombolo (prow. Padwy), który zaczął produkcję zdywersyfikowanego asortymentu polimerów inżynieryjnych, aż do otwarcia nowych oddziałów sprzedaży w Hiszpanii, Francji i Niemczech; od inauguracji Sirmax Polska w 2006 roku, do uruchomienia nowego zakładu produkcyjnego Sirmax do Brasil w Jundaì (San Paolo); od powstania Sirmax North America w Anderson (Indiana) w 2015 roku, po przejęcie fabryk Nord Color, włoskiego friulijskiego leadera w projektowaniu i produkcji specjalnych technopolimerów. W 2019 roku wybudowano drugi polski zakład w Kutnie, za to w roku 2020 przyszła kolej na drugą fabrykę w USA, w całości poświęconą obróbce tworzyw sztucznych pochodzących z recyklingu oraz na przejęcie Smart Mold, spin off-owego przedsiębiorstwa Uniwersytetu w Padwie – firmy inżynierskiej – objętej programem rozwoju i optymalizacji procesów produkcyjnych, mającej m.in. współdziałać z klientami w celu projektowania produktów poprzez wsparcie dla techniki formowania wtryskowego, zarówno w zakresie dotyczącym samego procesu, jak i produkowanych materiałów.
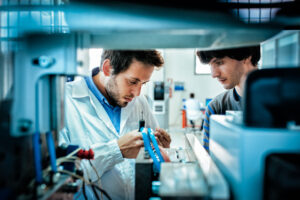
Jak ewoluował rynek tworzyw sztucznych w ostatnich latach, wziąwszy pod uwagę potrzebę tworzenia produktów zgodnie z zasadami zrównoważonego rozwoju?
Sirmax wszedł do branży tzw. zielonych tworzyw sztucznych w 2019 roku, przejmując SER, wysokiej jakości włoskie systemy w sektorze regeneracji poużytkowej tworzyw sztucznych, oraz MICROTEC, producenta kompostowalnych lub biotrwałych mieszanek, działającego głównie w sektorze folii opakowaniowych. W ten sposób firma jest w stanie sprostać wszystkim dyktatom zrównoważonego rozwoju, które dotyczą nie tylko produktów, ale obejmują także procesy, zarządzanie, waloryzację terenów, planowania przestrzennego, wzmacnianie kapitału ludzkiego. Rynek tworzyw sztucznych bardzo się rozwinął w ostatnich latach, wszyscy przedsiębiorcy zrozumieli, że zrównoważony rozwój jest nie tylko moralnym obowiązkiem i koniecznością, ale także czyni ich bardziej konkurencyjnymi. Dziś producenci samochodów lub sprzętu gospodarstwa domowego częściej proszą swoich dostawców o tworzywa sztuczne na bazie produktów pochodzących z recyklingu, nie zaś o te pierwotne. Ponadto wszyscy uczestnicy łańcucha dostaw zwracają uwagę na cały cykl życia samochodu czy urządzenia, skupiając uwagę, już na etapie projektowania, na dbanie o zasady zrównoważonego rozwoju podczas tworzenia produktu.
Ostatecznym celem stała się prawdziwa rynkowa cyrkulacja, w której produktom daje się coraz to nowe życia. Jeśli chodzi o materiał z recyklingu, to wygrywa on jeśli jest odpowiednio dostosowany, uszlachetniony. Oznacza to, że może mieć właściwości podobne lub wręcz identyczne z cechami pierwotnych tworzyw sztucznych. W tym miejscu do gry wchodzą badania, w które trzeba inwestować, znacznie więcej niż miało to miejsce w przeszłości. Sirmax koncentruje się właśnie na badaniach naukowych, starając się opracowywać produkty z części pochodzących z recyklingu, które są antybakteryjne, ogniotrwały (odporny na ogień), mają taką samą odporność na uderzenia jak pierwotny plastik i są bezwonne. Właśnie dzięki researchowi Sirmax może teraz mówić o tzw. upcyklingu, koncepcji wykraczającej poza zwykłą ideę recyklingu: jest to ponowne wykorzystanie wyrzuconych przedmiotów lub materiałów w taki sposób, aby powstał produkt o jeszcze wyższej jakości lub wartości niż sam oryginał.
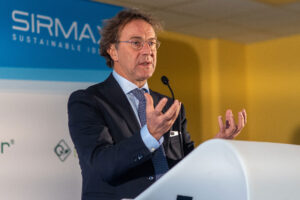
Jaki będzie plastik przyszłości?
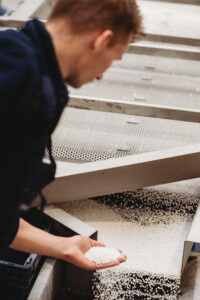
Będzie pochodził z recyklingu i nadawał się do kolejnego. Przyczyni się do zmniejszenia produkcji CO2 i do tworzenia coraz lżejszych podzespołów w sektorze motoryzacyjnym czy AGD. Sirmax ma już w swoim portfolio produktów kilka związków, które przyczyniają się do redukcji emisji CO2. Zleciliśmy firmie Spinlife, spin-off Uniwersytetu w Padwie, badanie oceny cyklu życia (Life Cycle Assessment) dwóch mieszanek polipropylenowych przeznaczonych dla sektora motoryzacyjnego i AGD: Isofilu, produkowanego z pierwotnego polipropylenu oraz Green Isofilu, zawierającego polipropylen z recyklingu „Serplene”. Oba produkty są mieszane z wypełniaczami mineralnymi, barwnikami i innymi dodatkami w różnych proporcjach. Stosując pokonsumencki polipropylen odzyskany z recyklingu, jako częściowy zamiennik pierwotnego, uzyskuje się znaczną redukcję w prawie wszystkich branych pod uwagę kategoriach negatywnego wpływu na środowisko. W szczególności, w zależności od zawartości frakcji poddanej recyklingowi w Green Isofil, emisje dwutlenku węgla można zmniejszyć o połowę, w porównaniu z produktem pierwotnym. Na podstawie tych działań, kierując propozycje asortymentu materiałów dla klientów można dążyć do większej dbałości o środowisko.
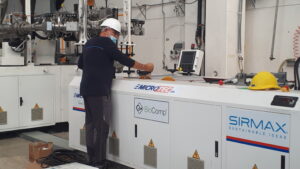
Jaką rolę na arenie międzynarodowej odgrywają włoskie i polskie firmy działające w tym sektorze?
Mogę opowiedzieć o roli Sirmax. Staliśmy się największym niezależnym producentem mieszanek polipropylenowych w Europie i piątym na świecie. Dużo zainwestowaliśmy w umiędzynarodowienie przedsiębiorstwa, aby skrócić łańcuchy dostaw i dzięki temu mamy zregionalizowaną i zaufaną sieć dostaw. To pozwoliło nam, szczególnie w ostatnich latach kryzysu pandemicznego i surowcowego, być bardziej elastycznymi niż duże koncerny i bardziej niezawodnymi niż mali dostawcy. Uważam, że tylko ze średniej wielkości strukturą, ale przy jednoczesnej elastyczności, szybkości i byciu blisko klienta, możemy odgrywać wiodącą rolę na świecie w tej branży.
Jak ważne są inwestycje Sirmax w Polsce?
Polska zawsze była strategicznym miejscem dla firmy Sirmax, od 2006 roku, kiedy wybudowaliśmy nasz pierwszy zakład typu greenfield, Sirmax Polska, zaawansowany technologicznie zakład produkcyjny w specjalnej strefie ekonomicznej w Kutnie koło Łodzi, przeznaczony do produkcji mieszanek polipropylenowych. W 2019 roku wybudowano drugi polski zakład, również w Kutnie, obok pierwszego, dedykowany produkcji elastomerów termoplastycznych z linii Xelter, do mieszanek technicznych, samogasnących i specjalnych technopolimerów. Pierwszy zakład o powierzchni 52 tys. metrów kw. (20 tys. m2 powierzchni produkcyjnej), jest zarazem największy w całym koncernie, jest w stanie produkować 85 tysięcy ton tworzyw sztucznych rocznie dla sektora motoryzacyjnego i AGD. Drugi zakład, dwunasty co do wielkości w koncernie, o powierzchni produkcyjnej 12 500 metrów kwadratowych, w całości dedykowany jest nowym produktom z rodziny Xelter. Łącznie w dwóch polskich zakładach zatrudnionych jest 130 pracowników. Bardzo zależy nam na Polsce, jej centralnym położeniu logistycznym i tym, że jest naszym przyczółkiem w kierunku Europy Wschodniej.
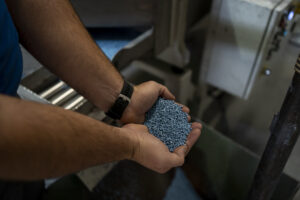
Dwa lata Covidu, a teraz wojna, wywołały negatywne skutki w wielu branżach przemysłu, jaka jest sytuacja w sektorze tworzyw sztucznych?
Nie mogę powiedzieć, że świat tworzyw sztucznych przez to wszystko nie ucierpiał. W obliczu Covidu zadaliśmy sobie pytanie, czy zatrzymać, czy też kontynuować rozpoczęte już inwestycje. Zdecydowaliśmy się jednak kontynuować, wzmocnieni szeregiem analiz rynkowych i pocieszających wskaźników, a także dzięki stabilności fi nansowej koncernu, która również odzwierciedla koncepcje zrównoważonego rozwoju i przejrzystości. Ta strategia nam się opłaciła. Rok 2020 okazał się wzrostowy pomimo pandemii Covid-19, dzięki silnemu ożywieniu zamówień w drugim półroczu. Potem nadszedł kolejny rok, który przeszedł wszelkie nasze oczekiwania, ze wzrostem z poziomu 300 mln przychodów w 2019 r. do 480 mln w 2021 roku. W sumie, inwestycje zrealizowane przez Grupę Sirmax w 2021 r. wyniosły około 24 mln euro: 12 z nich dotyczyło wzmocnienia obszaru Zielonej Gospodarki.
Pozostałych 12 dotyczyło nowego zakładu produkcyjnego w Stanach Zjednoczonych, co dopełnia łączną kwotę inwestycji, która od 2020 roku wyniosła około 30 milionów. W 2021 r. zatrudniono również 100 nowych osób, co dało łączny wzrost liczby pracowników z 700 do 800 na całym świecie. Nasze inwestycje oraz uprzywilejowanie zregionalizowanych i lojalnych łańcuchów dostaw sprawiły, że zdobyliśmy udziały w rynku. Byliśmy blisko klienta z dostawami, produktami ad hoc i zaawansowanymi technologicznie usługami, zawsze biorąc pod uwagę długoterminową perspektywę, budując wszystko z rozwagą i rozsądkiem. Obawy o przyszłość pozostają. Scenariusz geopolityczny, koszty energii i surowców mogą zmniejszyć popyt. Nie mam obaw o bezpośredni negatywny wpływ na Sirmax: nasze łańcuchy dostaw są zróżnicowane i pozwalają nam na budowanie zapasów zaopatrzenia. Niepokoi nas jednak pośredni wpływ na naszych klientów końcowych, w szczególności z sektora motoryzacyjnego, który jest szczególnie narażony i już osłabiony długotrwałym brakiem mikroprocesorów na rynku.